How will a mid-life upgrade keep the FAAM Airborne Laboratory at the forefront of atmospheric observations until 2040? MTI explores the tech behind the missions
Few airplanes boast a more colorful flight history than the FAAM Airborne Laboratory. The adapted Bae-146 research aircraft, operated by the UK’s National Centre for Atmospheric Science (NCAS) out of Leeds University, has skirted rumbling volcanoes, interrogated featureless oceans and dissected thundery desert cloud tops. Now, a US$60m UK government investment will propel FAAM onward to 2040.
“It’s a laboratory with every conceivable instrument, deployable virtually anywhere on Earth,” says Dr Chris Reed, technical coordinator at the Facility for Airborne Atmospheric Measurements (FAAM). “We can fly low and slow with lots of kit. We change the aircraft configuration and organize logistics, hotels – the whole package. We also fulfill a civil contingency role: if [UK Prime Minister] Rishi Sunak calls at 3am, we get up and fly.”
Such short-notice flights measured emissions from the 2005 Buncefield fire and 2010 Eyjafjallajökull eruptions. Based at Cranfield Airport, Bedfordshire, FAAM replaced the UK Met Office C-130 aircraft operated by the RAF under military designation until its retirement in 2004.
“Today, flying under normal airline designation allows us more freedom to operate,” says Reed. “We conform to passenger airline safety rules. UK Research and Innovation (UKRI) funds annual flight hours to allocate to researchers. The Met Office is a regular user. Private companies can contract us: for instance, an oil company wanting to measure fugitive oil rig emissions.”
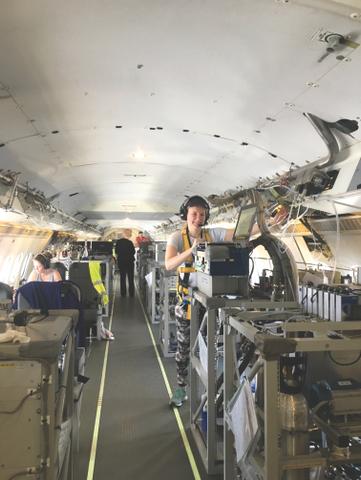
Technological abundance
In recent years, the FAAM aircraft has observed convective cloud microphysics in New Mexico and marine atmospheric self-cleansing mechanisms around Cape Verde. It has tracked ship exhaust plumes in the Atlantic, studied mixed-phase clouds in Labrador Bay and hunted chemical signals portending the eruption of Icelandic volcanoes. Researchers install specialized equipment on an aircraft already fitted with nearly 100 instruments and sensors.
“The instruments are the centerpiece,” says Reed. “The aircraft just moves them around. We have instruments to measure temperature, pressure and humidity very precisely. We couple high-data-rate pressure sensors with inertial and GPS navigation systems for accurate wind measurements. Most instruments have some redundancy. We like to measure things twice in different ways.”
FAAM uses chilled mirror hygrometers and optical absorption techniques to measure humidity. The hygrometers measure a frosted mirror’s reflectivity to enable humidity calculations, while optical measurements quantify water vapor based on laser attenuation.
“Chilled mirror hygrometers respond relatively slowly, with some hysteresis when ascending or descending,” continues Reed. “Our absorption system is less accurate, but very fast. In combination, they provide world-class in situ humidity measurements.”
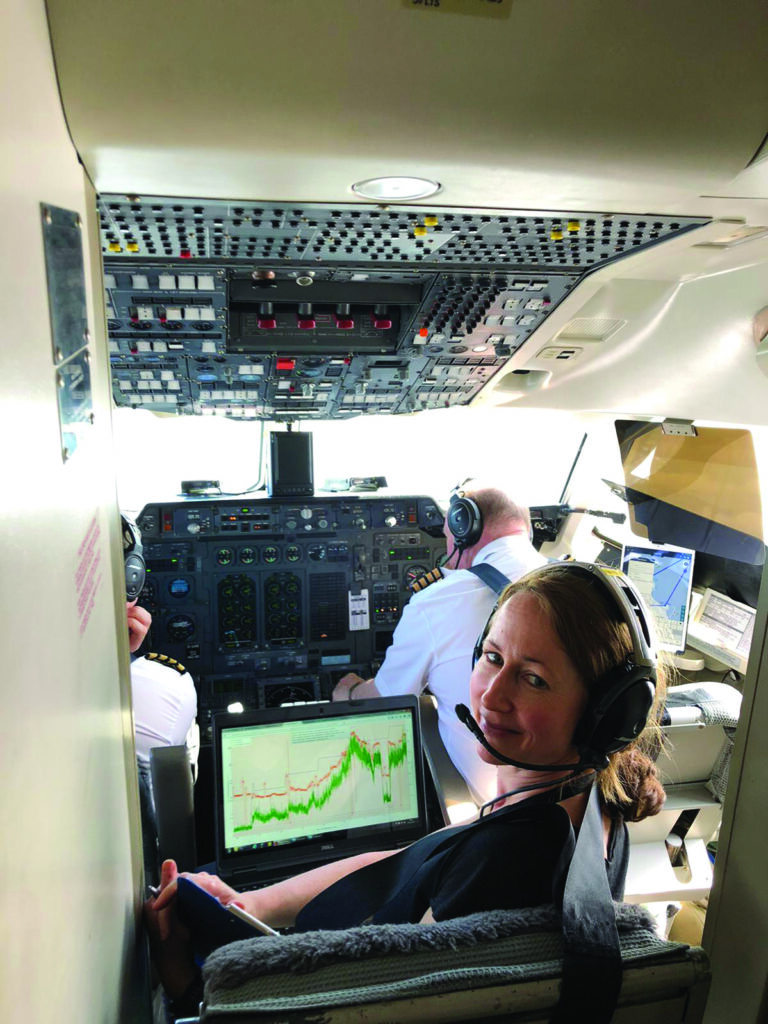
The Met Office uses the aircraft to study phenomena imperfectly represented in models. Cloud microphysics instruments fitted to wings provide in situ measurements. Forward-scattering of laser light from cloud particles captures size distributions up to 50μm. A much-requested passive cavity spectrometer probe measures aerosol particles from 100nm to 3μm. Imagers capture shapes and concentrations of particles traversing a laser beam, showing their individual ice habits.
“How ice is shaped is a function of the temperature and speed at which it formed,” says Reed. “It reveals a lot about processes in that cloud. Clouds contain astonishing numbers of droplets, but image recognition software can retrieve the ice habit from millions of images.”
Unique observations
The aircraft enables measurements that would be impossible by other means. Balloons collect useful vertical profile data but cannot be guided. Large drones may carry a 50kg payload but FAAM can fly 3.6 metric tons of instrumentation. The smallest cloud particles, invisible to ground-based dual-polarization radars, must be measured in situ. Inside convective clouds, balloons would be immediately rimed with ice and (along with drones) ejected by powerful updrafts.
“There’s no substitute for flying an aircraft into the cloud,” says Prof. Alan Blyth, project lead for the Deep Convective Microphysics Experiment (DCMEX) in New Mexico. “With four jet engines, the FAAM aircraft is powerful enough to pass through cloud turrets and rapidly climb to keep up with ascending cloud tops.”
DCMEX studied cloud microphysics above New Mexico’s Magdalena Mountains, an elevated heat island where convective clouds reliably form at the same time each day. This enabled Blyth’s team to precisely scan clouds with ground-based radars, measure particles at the mountain top and plan flights for systematic data collection without chasing clouds.
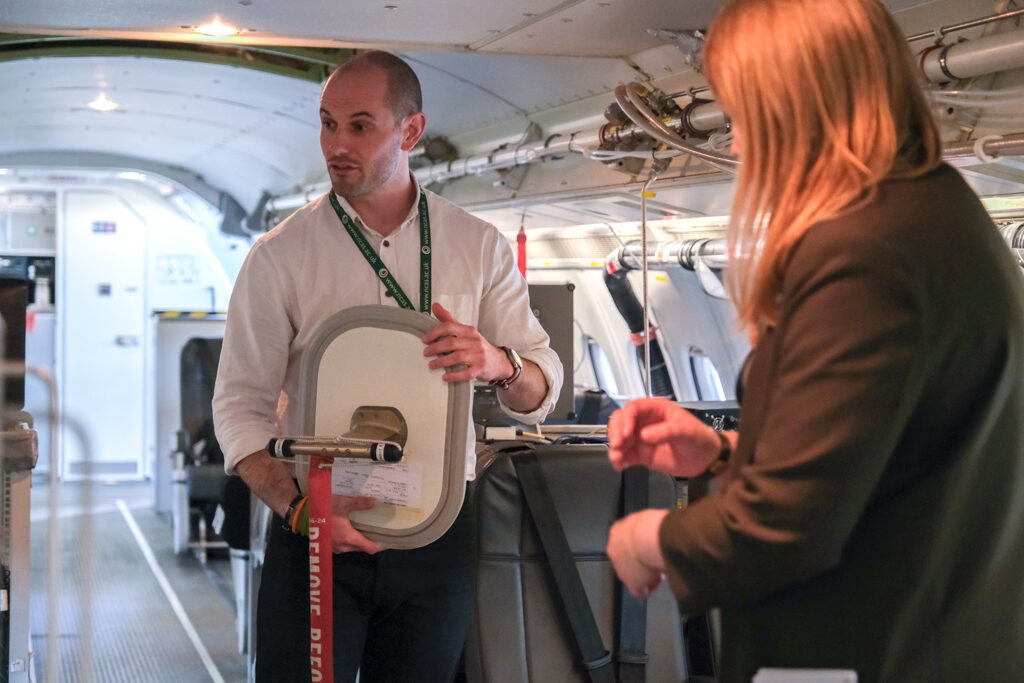
“Going through once only provides a snapshot,” says Blyth. “But we needed to understand the history of cloud particle development by following cloud tops growing higher and colder. We knew where clouds would form, pointed the aircraft at them and got the timing right.”
FAAM’s dropsonde system can release parachuted sensors every 30 seconds to provide high-frequency atmospheric profiles. An external radiation blister houses downward-looking radiometers and sometimes proof-of-concept satellite instruments ultimately destined for space. FAAM’s chemistry suite includes mass spectrometers and hybrid instruments such as laser ablation mass spectrometers, useful to campaigns like the Natural Environment Research Council (NERC)-funded ARNA (Atmospheric Reactive Nitrogen over the remote Atlantic) project.
“A drone could not have carried our state-of-the-art equipment,” says ARNA mission scientist Prof. Lucy Carpenter. “The aircraft allowed us to observe different air masses and explore humidity dependencies at altitude. The ability to fly close to the sea gave us great vertical profiles.”
“As a mission scientist, you sit behind the pilots,” she continues. “They will say, ‘What shall we do now?’ You see the raw data coming out in real time. I absolutely loved it.”
Maintenance and configuration
Carpenter also studies how tropospheric ozone deposits on the sea surface. The University of York is building a laser-based instrument to measure ozone in flux mode, which she hopes to fly on the aircraft. Reed leads a team of three engineers who build, modify and maintain FAAM’s own instruments, calibrated at institutes such as the National Physical Laboratory (NPL).
“Changing configuration requires coordination around other aircraft maintenance activities,” says Reed. “We fit instruments in external canisters, hardpoints and apertures. We have instruments in place of windows and many inside the cabin, plumbed to air sampling inlets. UK users can make next-day flight decisions but overseas campaigns require considerable planning.”
Researchers must first submit a proposal to use the aircraft which, according to Carpenter, is a year-long process with a 10% success rate. For DCMEX, there followed six months of preparation: preparing, checking then fitting instruments, performing test flights and planning logistics. FAAM makes reconnaissance visits to airports the aircraft will use and orchestrates peripheral elements, like booking hotels.
“That’s important because without proper rest, the project is at risk,” says DCMEX mission scientist Dr Keith Bower. “Because FAAM organizes all that, we can concentrate on the science. We send generic sortie briefs to Airtask, the contracted operator, then have a back-and-forth iteration. We organize ourselves into teams and have a rota so nobody gets overtired.”
NCAS operates several facilities besides the airborne laboratory. These include an observatory measuring air quality at London’s BT Tower, a Global Atmospheric Watch (GAW) regional station at Weybourne in Norfolk and a GAW global station in Cape Verde, Africa. The FAAM aircraft takes in situ measurements in conjunction with ground scans from the NCAS radar site in Chilbolton, Hampshire.
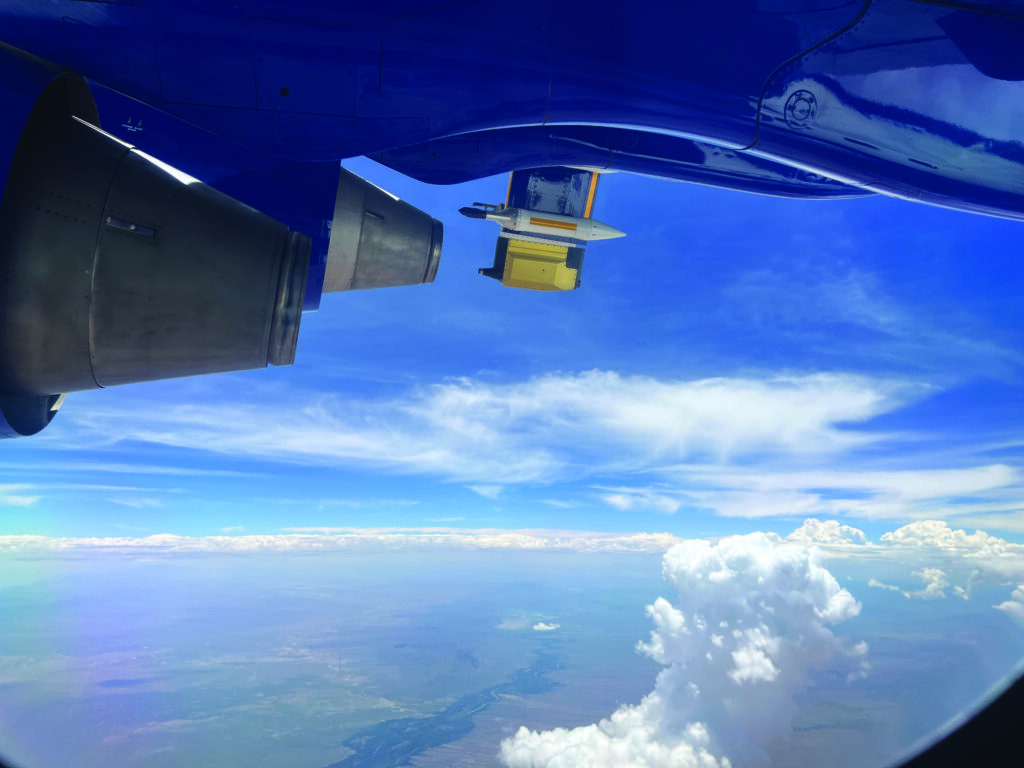
FAAM future
The UK government has allocated US$60m for a six-year mid-life upgrade project set to run until March 2026 and secure the aircraft’s future until the end of its lifespan in 2040. The project will encompass improvements to buildings and to an airframe that has already been stretched, re-engined and modified. New winglets may improve fuel efficiency, or new autopilot systems enable more complex approaches.
“We work with BAE Systems, the type certificate holder,” says Reed. “Fluid dynamic analysis of particle flow round the airframe will inform more rational positioning of instruments. Many instruments are outdated or no longer relevant – and there are new questions to answer. For instance, we want to understand indirect climate impacts related to the emerging hydrogen economy.”
Instrument miniaturization will of course save weight, and enhanced satcom bandwidth will enable ground-based remote control of instruments, so the aircraft will need to carry fewer people to push buttons. Power-efficient electronics will deliver increased data rates essential to obtaining meaningful measurements while moving at 115m/s.
DCMEX’s Bower was among the researchers who submitted successful proposals for new instruments within the mid-life upgrade. “We’ll get a new instrumentation suite we couldn’t normally afford,” says Bower. “We’ll upgrade our workhorse 2D stereo probe. A new probe, Hawkeye, will incorporate four spectrometers to measure cloud particle size distributions. There’s a stereo version of our high-volume precipitation spectrometer, a holographic spectrometer and a particle habit imaging and polar scattering probe, taking us into a new realm of polarimeter measurements.”
Flying into developing convective storms carries an elevated risk of lightning strikes. Experts monitor the electrical field from the ground and tell the aircraft when it’s time to leave. Bower, a 250-flight FAAM veteran, has nonetheless experienced several lightning strikes.
“There’s so much noise and light, you think the whole aircraft has exploded,” he says. “Actually, you’re pretty safe because it’s a Faraday cage but exposed equipment can get damaged. Cloud probes are the worst – out on the wings, just waiting to be hit.”
Every flight is meticulously planned for safe operation with appropriate mitigation of risks. Bower is fulsome in his praise of Airtask pilots, who he says do their utmost to enable the required science while always remaining within the bounds of safety. Reed, meanwhile, takes assurance from the aircraft’s robustness and a shared sense of professionalism.
“We trust the pilots and engineers,” he says. “We do safety training. Everybody knows their job. A window cracked once, flying into clouds at Cape Verde. Nobody panicked; the pilot just said, ‘Sorry folks, we’ll have to go home.’ That window is a coffee table in our office now.”
This article originally appeared in the April 2023 issue of Meteorological Technology International. To view the magazine in full, click here.